
“In OASES, each task can have the required material listed and specified as required or contingency against likely findings from the task,” Frost remarks. For him, a key element is for the organisation to know what materials are required for maintenance activities.
#Mro inventory meaning software#
Likely to agree wholeheartedly with Downes’ suggestion to use a “good maintenance software programme” is Adam Frost, product manager for OASES. We have a continual investment in software, which positions APOC as a frontrunner in the sector ready to support the renewed growth in the USM (used serviceable material) market.” “At APOC, we are continually evolving our software and real-time stock data and we have positioned ourselves to exceed market predictions and expectations. “Although it is crucial to have a supply chain and inventory plan to avoid costly parts shortages, not many airlines can get it down just right, as it is tricky to formulate a strategy on their own in this unpredictable economic climate,” she says.
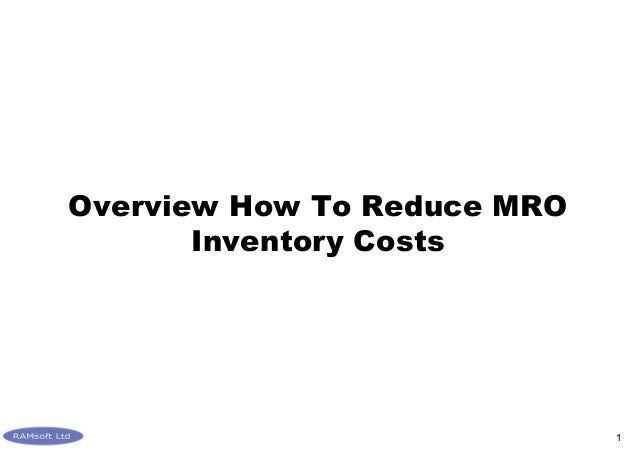
#Mro inventory meaning free#
By identifying their parts procurement cycles in advance, while ensuring precise budget and capital flow planning, both airlines and manufacturers can optimise operations and free up their cash flow for other investments.”ĭownes says it’s also important to consider how valuable the use of a good maintenance software programme can be to assist with managing spare parts inventory. Plan ahead by mapping out consumption requirements and forecast the parts needed to tie in with their longer-term company objectives. The best way for an airline to overcome supply chain shortages is not with short-term fixes, but by taking a long-term perspective and accurately identifying their present and future needs for parts. “By working with a third-party parts supplier, airlines can consolidate their purchases while still ensuring access to aircraft parts as and when required.”ĭownes continues: “Another essential aspect is to forecast the customer’s parts consumption and needs. With a proper system in place, airlines can reduce the capital burden of holding inventory and so free up cash flow,” she emphasises. “One of the most important is to set up a profitable inventory management structure.
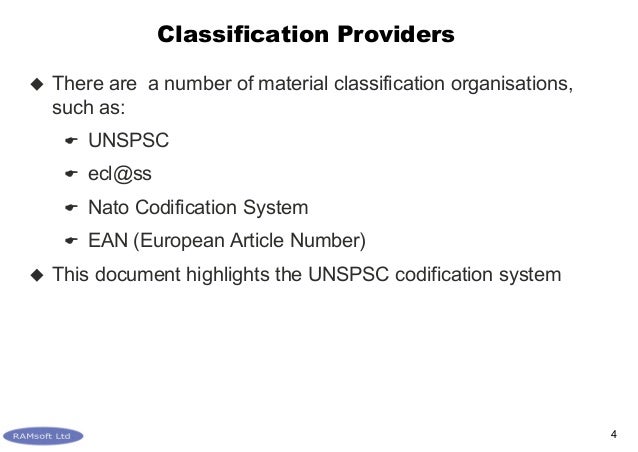
Tracey Downes, head of component sales for APOC, confirms that there are a number of elements to consider. It’s a tough task getting the right balance, and those charged with doing so – be they in-house airline maintenance departments or third-party MRO providers – have their views on the key elements for managing spare parts inventory. The field of aircraft spare parts inventory management highlights the occasions when having enough spares in house keeps the business running, but having too many can make life tricky by tying up capital.
